ABSTAPELSYSTEM für Fronten und Strangware
Das Abstapelungssystem für Fronten oder Strangwaren arbeitet mit zwei Robotern, die im Auslauf von Kantenanleim- bzw. Bearbeitungsanlagen eingesetzt werden.
Die Fronten können dabei auf unterschiedliche Ablageplätze gestapelt werden, wobei die Roboter auf drei der Ablageplätze abwechselnd zugreifen können. Das heißt auf den mittleren Plätzen können beide Roboter im Wechsel Werkstück für Werkstück abstapeln. Die Strangware wird auf einem großen zentralen Ablageplatz abgelegt.
Diese Roboterapplikation kann unabhängig vom Hersteller der Kantenbearbeitungsanlagen eingesetzt werden. Die Leistung der Anlage liegt bei bis zu 30 Fronten und 14 Strängen pro Minute.

ROBOTERGESTÜTZTE KOMMISSIONIERUNG
von Hoch-, Ober- und Unterschrankseiten
In diesen Anlagen kommissionieren Palettierroboter anhand von Auftragslisten diverse Schrankseitentypen zu Stapeln für die spätere Fertigung. Die Roboter arbeiten auf von uns entwickelten Linearachsen und greifen auf eine beliebige Anzahl von Seitenstapeln zu.
Die Gesamtanlage fordert die notwendigen Eingangsstapel über die übergeordnete Steuerung bei der Logistik an. Nachdem die Seitenstapel an das Zuführtransportsystem übergeben sind, werden sie innerhalb der Anlage vollautomatisch auf den entsprechenden Rollenbahnen den Robotern zur Verfügung gestellt. Dieses wird durch diverse Transporte und durch integrierte Querfahrwagen realisiert.
Die Roboter bewegen sich mit so genannten Tenderwagen. Auf diesen legen die Roboter jeweils die Seiten zu kommissionierten Stapeln zusammen. Die gebildeten Stapel werden an das angeschlossene Ausgangsstapel-Transportsystem übergeben.
Ein großer Vorteil dieses Systems ist die niedrige Bauweise, so dass das System auch unter Bühnen oder in zwei Ebenen aufgebaut werden kann.

ROBOTER-SETZSTATION
für Schrankaufhänger und Aufhängeschiene
Diese patentierte Roboterapplikation setzt sogenannte "verdeckte Oberschrank-Aufhänger", die hinter der Rückwand montiert werden, in den vorgepressten Korpus. Zusätzlich setzt der Roboter danach die Aufhängeschiene in die vorgesehen Transportfixierung.
In der darauf folgenden Korpuspresse können die Schrankaufhänger seitlich unter 45 Grad automatisch verschraubt werden. Die Schrankaufhänger – rechte und linke Ausführung – werden aus zwei Sortiertöpfen bereitgestellt, die Aufhängeleisten werden aus Magazinen vereinzelt.
Der Roboter übernimmt die Aufhänger und greift zusätzlich die Aufhängeschiene. Parallel läuft der Korpus in die Station ein und wird ausgerichtet. Beim Einsetzen der Beschläge bringt er zunächst die Aufhänger nacheinander ein, um dann die Wandbefestigungsleiste in die Transportsicherung der Aufhänger zu fixieren.
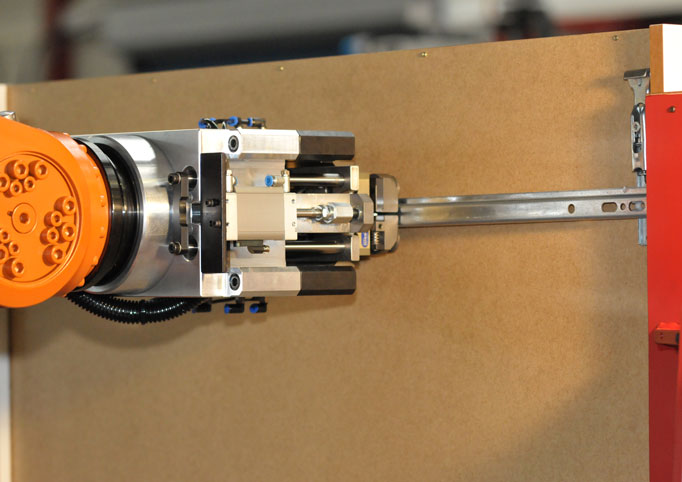
KOMMISSIONIEREN UND SETZEN
von Klappenbeschlägen
Zwei Roboter arbeiten in der Anlage parallel. Ein Roboter kommissioniert die Klappenbeschläge, der andere setzt diese auf die Korpusseiten. Um die genaue Position zum Setzen des Klappenbeschlags zu ermitteln, vermisst der Roboter vorab die Bohrungen zueinander und berechnet die Setzposition neu. So können die Klappenbeschläge exakt positioniert werden.
Der Kommissionier-Roboter (Bild hinten) entnimmt die Klappenbeschläge aus Kunststofftrays und legt diese in einen Zwischenpuffer. Um möglichst viele Trays erreichen zu können, verfährt der Roboter auf einer von uns entwickelten siebten Achse.
Der zweite Roboter nimmt die sogenannten Kraftspeichermodule aus den Zwischenpuffern. Er fährt über einen Scanner zur Plausibilitätskontrolle, anschließend wird die Komponente im Greifer ausgerichtet. Wenn der Klappenbeschlag richtig im Greifer liegt, fährt der Roboter weiter zur bereits ausgerichteten und gespannten Korpusseite.
Hier tastet er die notwendigen Bohrungen ab, um dann mit Hilfe der gemessenen Bohrpositionen, die ideale Setzpotion zu berechnen und diese entsprechend zu korrigieren.
Im Nachgang werden die Klappenbeschläge verschraubt.
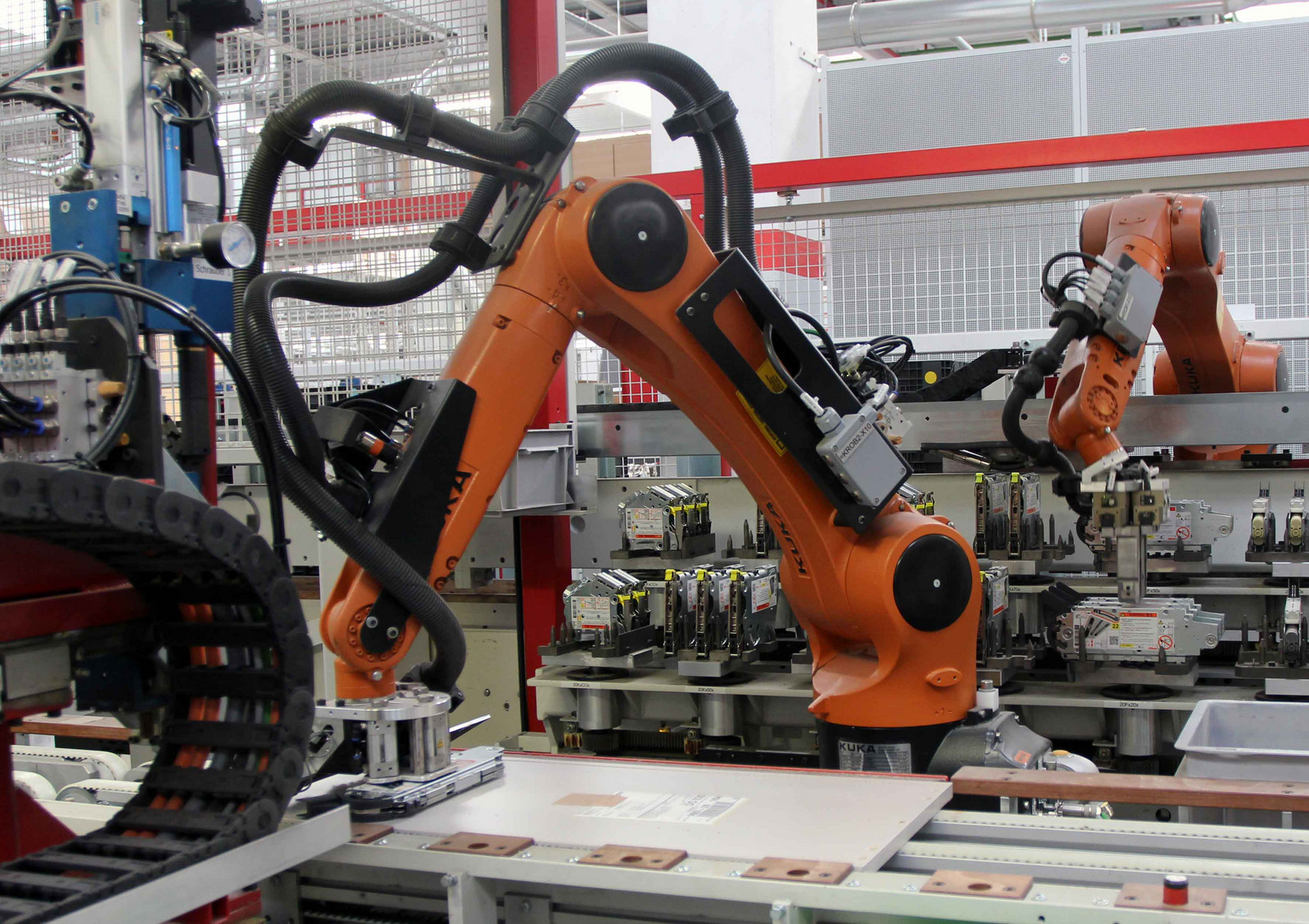
Roboter-Bearbeitungsanlagen für
GLASRAHMENFRONTEN
In diesem Fertigungssytem werden Glasrahmenfronten durch zwei Roboterzellen vorbereitet, durch manuelle Montage komplettiert und in einer Endmontagepresse fertiggestellt. Über einen Igelpuffer werden die vorgefertigten Fronten für die Gesamtanlage bereitgestellt. Die Fronten sind zu diesem Zeitpunkt bereits gebohrt. Außerdem sind Beschläge, wie Topfbandschaniere und Dämmpuffer, gesetzt.
In der ersten Zelle bearbeitet der Roboter die Front mit mehreren Werkzeugen. Zunächst bohrt er die Front vor, um anschließend den Ausschnitt für das Glaselement zu fräsen. Der zweite Roboter setzt die Befestigungsleisten für den Glaseinsatz vollautomatisch ein und fixiert diese mit einem Klammergerät.
Nach der Kunststoffleistenmontage folgen Handarbeitsplätze für die Endmontage der Glasrahmen-Fronten. In der Endmontagepresse werden die Kunststoffleisten endgültig ausgerichtet und verpresst.

SCHUBKASTENMONTAGETECHNIK – System Hettich
Bei diesen Montagesystemen handelt es sich um flexible Teil- bzw. Komplettlösungen für die automatisierte Montage von Rück- und Seitenwänden sowie der Schubkastenfronten. Durch die automatische Breiten- und Tiefenverstellung wird eine Schubkastenfertigung mit der Losgröße 1 realisiert.
Diese Montagelinien sind speziell für Schubkastensysteme der Firma Hettich entwickelt worden. Neben den direkten Montageeinheiten beinhalten die Anlagen auch die Magazinierung und die Bereitstellung der Einzelteile.
Parallel zur Montage der Schubkästen werden die Fronten gebohrt und die entsprechenden Beschläge gesetzt. Schließlich wird der Schubkasten mit der Front vereint.

ROBOTER-MONTAGEKOPF
für das Einsetzen von Glasfronten-Dichtprofilen
Dieser Roboter setzt endlos Dichtprofil von einer Rolle in unterschiedliche Glasfronten ein und schneidet dabei das Dichtprofil individuell auf Maß und Gehrung zu.
Die Glasfronten werden manuell in die Frontenaufnahme gelegt und über das Wechseltischsystem in die Fertigungszelle eingefahren. Der entscheidende Faktor in diesem System ist der selbst entwickelte Montagekopf für das Dichtprofil.
Dieser Montagekopf besteht aus einer Vorschub- und Führungseinheit, verschiedenen pneumatisch gesteuerten Eindrückrollen und einem pneumatisch betätigten Schneidmesser für das Handling und die Bearbeitung des Dichtprofils, sowie einem 3D - Messtaster für die Erfassung des Glasauschnittes.

ROBOTERGESTÜTZTE KLEBEAPPLIKATION
für Reversionsklappen
In dieser Fertigungszelle werden vorgefertigte Aluminium-Rahmen auf Gipskartonplatten unterschiedlicher Größen aufgeklebt. Dabei werden die Rahmen durch die manuelle Beschickung über ein Transportband zugeführt, während die unterschiedlichen Gipskartonplatten palettenweise in einem Aufnahmegestell zur Verfügung gestellt werden.
Durch die automatische Erkennung der Rahmengröße wird durch den Roboter eine entsprechend große Gipskartonplatte von einem der Palettenstapel geholt, an der Ausrichtstation ausgerichtet und an einer Klebepistole entlang geführt.
Im nächsten Schritt wird die Gipskartonplatte auf den Montagetisch gelegt und fixiert, der Aluminium-Rahmen vom Transportband geholt und darauf gelegt. Danach wird der Rahmen für einige Sekunden auf die Platte gedrückt. Anschließend wird die fertige Reversionsklappe auf das Transportband für den Austransport abgelegt.
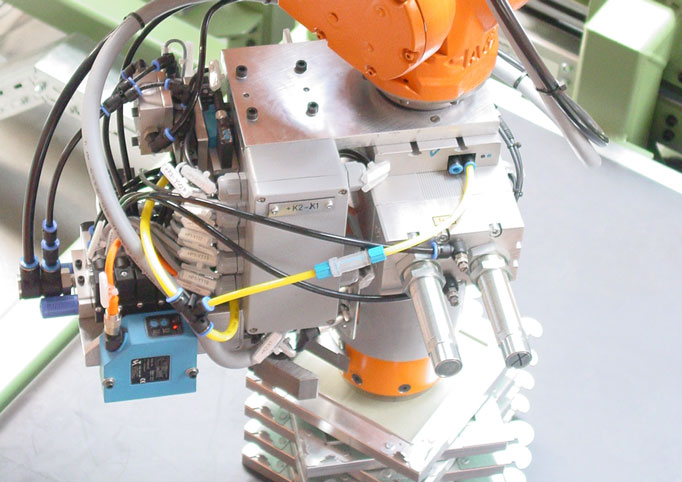
ANLAGENBESCHICKUNG mit Roboter
Im Bereich der Anlagenbeschickungen übernehmen die Roboter nicht nur das Werkstückhandling, sondern auch für das Handling der Schonerplatten, Trays/Formnester, Paletten oder weiterer Verpackungsbehälter genutzt.
In Frontenbearbeitungsanlagen übernimmt der Roboter beispielsweise das Handling der Möbelfronten (Bilder rechts oben). Der Roboter entnimmt die vorkommissionierten Fronten aus einem Fronten-/ Hordenwagen und legt diese in die Anlage ein. Die bearbeiteten Möbeltüren stellt der Roboter schließlich in den Frontenwagen zurück oder legt diese für die manuelle Nacharbeit in einen Igelpuffer ab.
Roboter zur Bereitstellung von Schubkastenschienen sind in Korpusmontagelinien für Unterschränke integriert. Die Roboter entnehmen die Schubkastenschienen aus den Trays lagenweise und legen diese in Puffermagazine ab. Die Trays mit den Schubkastenschienen werden auf Paletten gestapelt und über Rollenbahnen in die Roboterzelle eingebracht. Der Roboter misst die Position der Trays ein, entnimmt die Schubkastenschienen, handelt das leere Tray oder die leere Paletten.
Eine andere Roboterapplikation (Bild rechts unten) stellt Schubkastenrückwände für die Montagestation bereit. Auf Grund der großen Typenvielfalt muss der Roboter auf viele verschiedene Rückwandmagazine zurückgreifen. Deshalb fährt der Roboter auf einer selbstentwickelten siebten Achsen an den Rückwandmagazinen entlang.

Weitere ROBOTER-PROJEKTE
- Schubkastenschienen-Handling
- Pick & Place von Schubkastenschienen
- Setzstation für Sockelfußadapter mit Roboter
- Bereitstellung von Sockelfußadaptern
- Dübel-Bohrautomat mit Roboterhandling